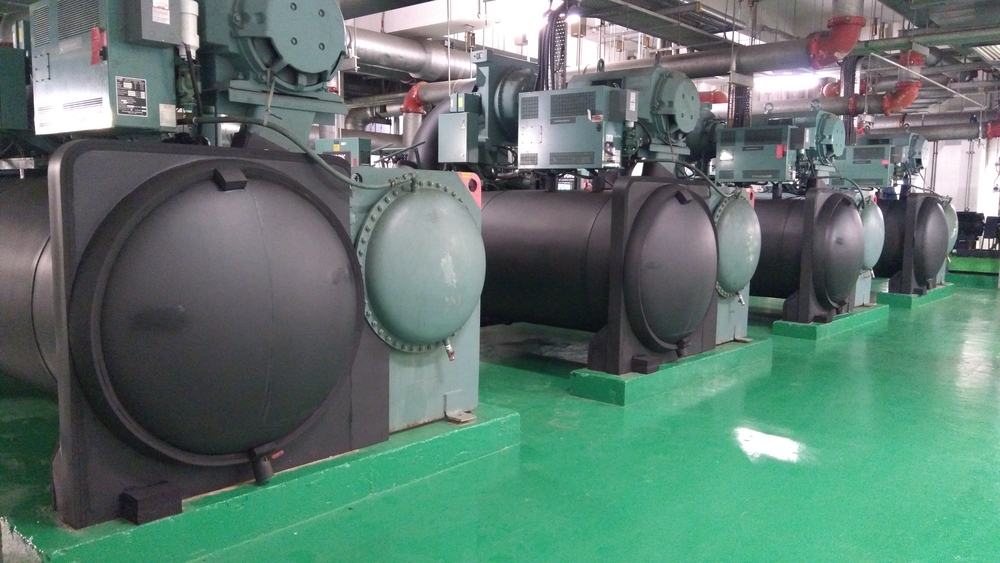
Water chillers industrial are common pieces of equipment that are used to regulate temperature in a variety of applications. Water chillers industrial are typically found in HVAC systems, and they are also commonly used within industrial applications to cool high precision machinery and provide a stable ambient temperature for certain types of specialized equipment.
Water chillers industrial work on the same basic principles as air conditioning units, refrigerators, and freezers, although there can be some variations in size, efficiency, and the substances used to collect and reject heat from an environment.
Water chillers industrial function is based on a fairly simple concept, but it is important to first grasp the fundamentals of this concept in order to have an understanding of how water chillers industrial are able to carry out their purpose.
Heat Transfer and Water Chillers Industrial
If you’ve ever flipped on a window air conditioning unit and stood next to it waiting for it to begin blowing out cold air, then you’ve probably noticed that it generates a fair amount of heat before producing cold air.
This may seem counterintuitive at first, but once you understand that cooling units work based on transferring heat, rather than producing cold, this will start to make more sense.
But before we get into how this works, we need to go over the essential parts of water chillers industrial and what they do.
Refrigerant
Also known as coolant, this is the substance that circulates throughout the water chillers industrial system to collect and reject heat from the water that is being used to cool a machine or environment.
There are a few different types of coolant, but there are a couple in particular that are gaining popularity because they have a lower environmental impact in comparison to older types of refrigerant.
Refrigerants have special properties that allow them to transfer heat extremely quickly, and the entire water chillers industrial process is based around these properties. What allows refrigerants to transfer heat so efficiently is their incredibly low boiling points.
When a substance boils, like water for example, the molecules within that substance begin to become excited as heat is transferred into the substance. This heat transfer results in increased kinetic energy among the molecules, causing them to move more quickly. The faster these molecules move, the more they will start to collide with one another, eventually resulting in the molecules being pushed out of the substance and into the air as water vapor.
The boiling temperature for water is 212º Fahrenheit and 100º Celsius, so once water reaches this temperature, it will begin to turn from a liquid into a gas. It’s important to note that the lower the atmospheric pressure, the lower the boiling point will be. So while water boils at 212º F while at sea level, it will boil at a significantly lower temperature on the top of Mt. Everest. We will return to this point later when talking about condensers.
Once you turn off the burner on your stove, it will almost immediately stop bubbling, but it will continue to steam for a while. What is happening here is that the heat applied to the water is being transferred in the form of kinetic energy. As the water continues to steam, it is continuing to push water molecules out, and these molecules take some of that kinetic energy with them. Eventually, once enough kinetic energy has been transferred, the water’s temperature will normalize with its surroundings.
The same thing happens with refrigerants, but, since the boiling point for refrigerants is so low (around -15º Farenheit), it will transfer heat in the form of kinetic energy much more quickly and efficiently than water, creating a much faster equilibrium in temperature.
If you’re still not sure how boiling a substance can cause a cooling effect, this concept will start to make more sense as you continue to read.
Compressor
Water chillers industrial are closed-system cooling units that go through a continuous and circular process to transfer heat from a particular substance. Because all of the components of water chillers industrial are constantly cycling through and feeding the next component, it’s difficult to say where the process begins and ends. However, for the purposes of understanding the whole process, it’s best to start with the compressor.
When refrigerant circulates into a compressor, it is in a gaseous state. Once the refrigerant is inside the compressor, mechanical force is applied to the refrigerant within a confined space in order to compress the gas into a superheated state. When this happens, the molecules are pushed closer together, causing the refrigerant molecules to collide into each other, which increases the amount of kinetic energy in the substance.
As the kinetic energy of the refrigerant molecules increases, the substance becomes extremely hot. This is a process known as adiabatic heating.
Once the compressor has fully compressed the refrigerant into its superheated gaseous state, a valve is opened, allowing the refrigerant to move to its next stop in the cooling process.
Condenser
The condenser is a crucial step in the process because it causes the refrigerant to undergo a change in its physical state, as well as its temperature. Remember that refrigerant has an extremely low boiling point, so it wants to be in a gaseous state. But for it to give us a cooling effect, we need it to be in a liquid state so it can boil and transfer heat away from our water lines, giving us nice, cool water to cool our machines.
Do you recall what we said before about boiling points and pressure? The lower the pressure is, the lower the boiling point will be. Well, this principle also works conversely: the higher the pressure, the higher the boiling point will be.
Remember that when our refrigerant moves into the condenser, it is still under a high amount of pressure, so at this point, its boiling temperature has been significantly increased, allowing it to turn back into a liquid much more easily.
Inside the condenser, the refrigerant comes into contact with an enclosed water line that is carrying a flow of warm water. As the refrigerant makes contact with the water line, much of its kinetic energy is transferred to the water through the walls of the water line, which will typically be made from a highly conductive material like copper.
By transferring its thermal energy to the water through the pipe walls, the refrigerant is able to condense into a semi-liquid state. You might think of the way that a cold glass of water will sweat on a warm day. Water vapor from the atmosphere condenses into a liquid as its temperature drops. Our refrigerant is doing the same thing inside the condenser.
After our refrigerant undergoes this physical state change, converting from a hot, high-pressure gas into a cooler semi-liquid state, the refrigerant is then ready to move on to the next stage in this cycle.
Expansion Valve
When the refrigerant makes it to the expansion valve, it is still under quite a bit of pressure, even though its temperature has dropped significantly. The function of the expansion valve is to reduce some of that pressure, which allows the refrigerant to cool off some more.
An expansion valve is simply a valve that allows the refrigerant to move into a space where it can expand at a controlled rate. Without the expansion valve, our refrigerant would expand too quickly and revert back into a gaseous state, which would cause it to cool our water line less efficiently.
To give this idea some visual context, imagine a group of people who are trying to pass through a turnstile. Since everyone in the group has to pass through a single point one at a time, the group of people will amass on one side of the turnstile, which results in a higher concentration or pressure on one side.
As people make their way through, they will disperse as they go their separate ways, resulting in a much less dense mass of people.
The expansion valve on water chillers industrial function in a similar way. As the pressurized refrigerant is pushed against the expansion valve, it amasses on one side of the valve. Then the valve begins to let the refrigerant through at a controlled rate, allowing the refrigerant to expand into a less dense mass. This expansion will cause the refrigerant to give off some of its thermal energy, while still keeping it in a semi-liquid state.
Have you ever powered up an air compressor and touched the metal tank as the pressure increased? If you have, then you probably noticed that the tank felt pretty warm to the touch. However, something that seems kind of strange happens when you finish using the compressor and open the valve to let the air escape.
The valve usually becomes covered in ice when the air is allowed to escape quickly. This may seem somewhat counterintuitive to think that a hot, pressurized gas will come out extremely cold, but this goes back to what we said about the transfer of heat.
When most substances are compressed, the molecules become excited as they have less room to move around, causing them to bump into each other much more frequently, which raises the thermal energy of the substance significantly. But when the substance is depressurized quickly, those same excited molecules are able to quickly disperse, taking all of their thermal energy with them and causing a notable cooling effect.
This is known as adiabatic cooling, and the expansion valve provides a similar effect in a more controlled manner.
As our refrigerant passes through the expansion valve and collects in its semi-liquid state, it is now ready to move into the evaporator.
Evaporator
The evaporator works in a fashion similar, yet converse, to the condenser. Instead of the water taking the thermal energy from the refrigerant, the refrigerant is taking the thermal energy from the water.
As the semi-liquid refrigerant collects around the water pipe that flows through the evaporator, the refrigerant is heated by the warm water that is running through the pipe. This causes the refrigerant to quickly boil and evaporate, taking the thermal energy of the water with it.
This process happens so quickly and efficiently that the refrigerant is able to significantly cool the water as it passes through the evaporator. And once the refrigerant reverts back into its gaseous state, it is ready to start the process all over again.
Water Chillers Industrial in Manufacturing
Now that we have a detailed understanding of how water chillers industrial work, let’s look at some of the ways that water chillers industrial are used in the manufacturing process.
Injection Molding Machines
Plastic injection molding is the process of injecting a melted plastic into a mold, which will then harden inside the mold to take on the desired shape. This process is used to create a wide variety of products, such as water bottles, furniture, electronics components, medical devices, and the list goes on.
Water chillers industrial are used in the injection molding process to cool the mold and the air that is injected into the plastic within the mold. By maintaining a stable temperature, manufacturers can ensure that their products are consistent and free of deformities.
Laser Cutting Machines
Industrial laser cutting machines also employ water chillers industrial to regulate the temperature of their laser tubes and ensure a stable performance.
CNC Machines
CNC (Computer Numerical Control) machines often have water chillers industrial incorporated into their components as well. Water is used to cool the machine and regulate the temperature of their cutting tools, which reduces wear and tear and improves cutting accuracy.
Plasma Cutting Machine
Another cutting tool that produces a significant amount of heat is the plasma cutter. Water chillers industrial are used to cool the plasma torch during the cutting process to prevent overheating and enhance its accuracy.
These are just a few of the many industrial machines that require water chillers industrial to regulate and improve their performance.
IndustryNest
If you are in need of water chillers industrial or anything else for your manufacturing process, give us a call to speak with one of our experienced representatives.
Just have a quick question or maybe one requiring some additional expertise? You can also visit our forum and get expert advice from real engineers.